MultiCollector® II: Smart Data Management for Multi-Instrument NDT Systems
Automated, centralized data collection and traceability across your NDT production lines
MultiCollector® II is MAC’s intelligent data storage solution designed to simplify and optimize test data management in high-volume, multi-instrument NDT environments. Built for compatibility with a wide range of MAC® instruments, MultiCollector® II seamlessly collects, stores, and organizes test data into a secure, SQL-based platform—providing operators with immediate access to detailed test records, quality trends, and production traceability across the entire network.
Whether you are running a single test station or managing multiple lines with a combination of ultrasonic, eddy current, and flux leakage systems, MultiCollector® II empowers your team to track results, generate reports, and maintain quality standards—faster and more efficiently than ever before.
Key Features & Capabilities
Automated Data Collection
Eliminates manual logging by automatically capturing test results from connected MAC® instruments and organizing them into one centralized SQL database.
Multi-Instrument Synchronization
Supports integration with Echomac®, MultiMac®, Rotoflux® AC, Varimac®, and Production Comparator VI systems—ensuring cohesive, system-wide data collection and streamlined oversight.
Complete Product Traceability
Tracks each individual part with unique IDs and links test results, defect data, operator logs, and equipment settings to enable full traceability and compliance documentation.
Integrated Report Generator
Create customer-ready reports with the embedded Report Generator. Users can pull data using MAC’s preloaded templates or design custom formats tailored to specific customer requirements.
Network-Wide Access
Authorized users can access MultiCollector® from any workstation on the network, enabling faster follow-up analysis, test verification, and QA review from multiple locations.
Optimized for Weld Line Applications
MultiCollector® II is ideal for weld line inspections where test data from multiple inspection points—such as weld zone and body—must be consolidated and analyzed quickly. The system’s ability to monitor, collect, and trace defects at each stage ensures early issue detection and minimizes costly rework.
Comprehensive Test Data Insights
-
Defect location, type, and severity
-
System and operator settings at time of test
-
Equipment logs and channel parameters
-
Time-stamped data for every test event
-
Folder-based organization for each tested piece
MultiCollector® II is a powerful tool for quality assurance teams seeking more control, visibility, and reliability in their data-driven environments.
Technical Highlights
-
Database Type: Open SQL
-
Compatible Systems: Echomac®, MultiMac®, Rotoflux® AC, Varimac®, Production Comparator VI
-
Report Templates: Built-in MAC® templates + custom options
-
Access: LAN-based, multi-user accessibility
-
Traceability: Unique part tracking with test and operator logs
-
Export Options: CSV, PDF, custom formats
Applications
-
Centralized Data Management for NDT Test Systems
-
Quality Control & Compliance Reporting
-
Product Traceability & Certification
-
Weld Line Data Consolidation
-
High-Volume Production Monitoring
Reliable, Field-Tested Software Integration
MultiCollector® II is built with the demands of industrial inspection in mind. With intuitive operation, compatibility across multiple MAC systems, and support from our global service network, MultiCollector® II offers long-term reliability and performance in even the most demanding environments.
You may also like
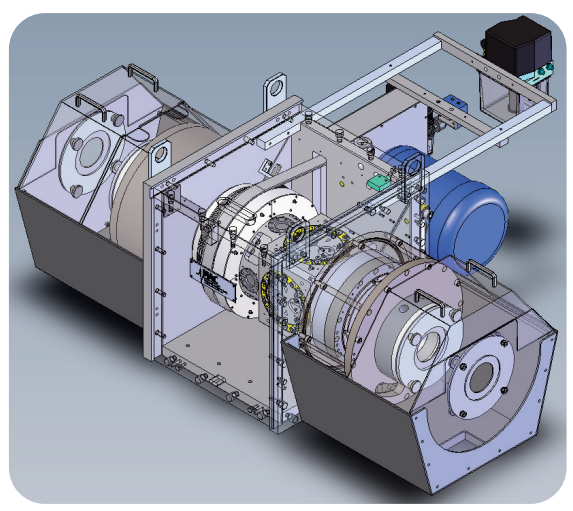
Ultrasonic Rotary Mechanism for High Speed Testing of Round Bar and Tubular Products
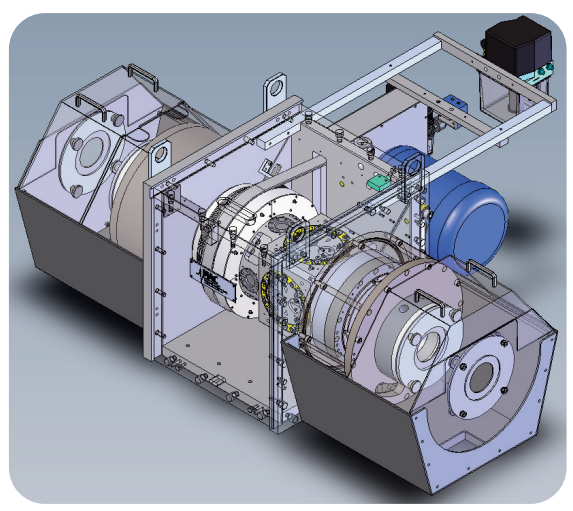
Ultrasonic Rotary Mechanism for High Speed Testing of Round Bar and Tubular Products
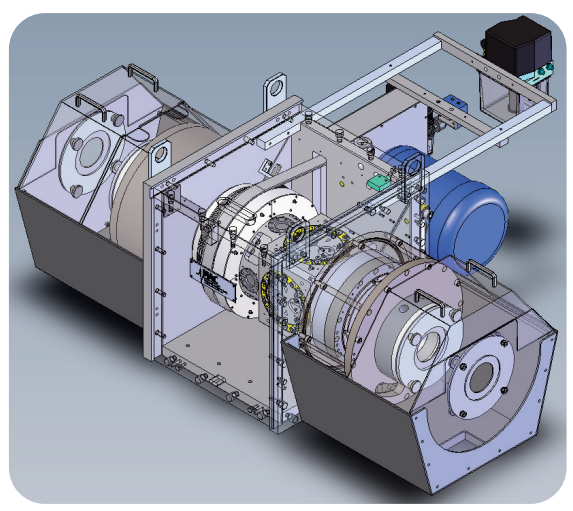
Ultrasonic Rotary Mechanism for High Speed Testing of Round Bar and Tubular Products
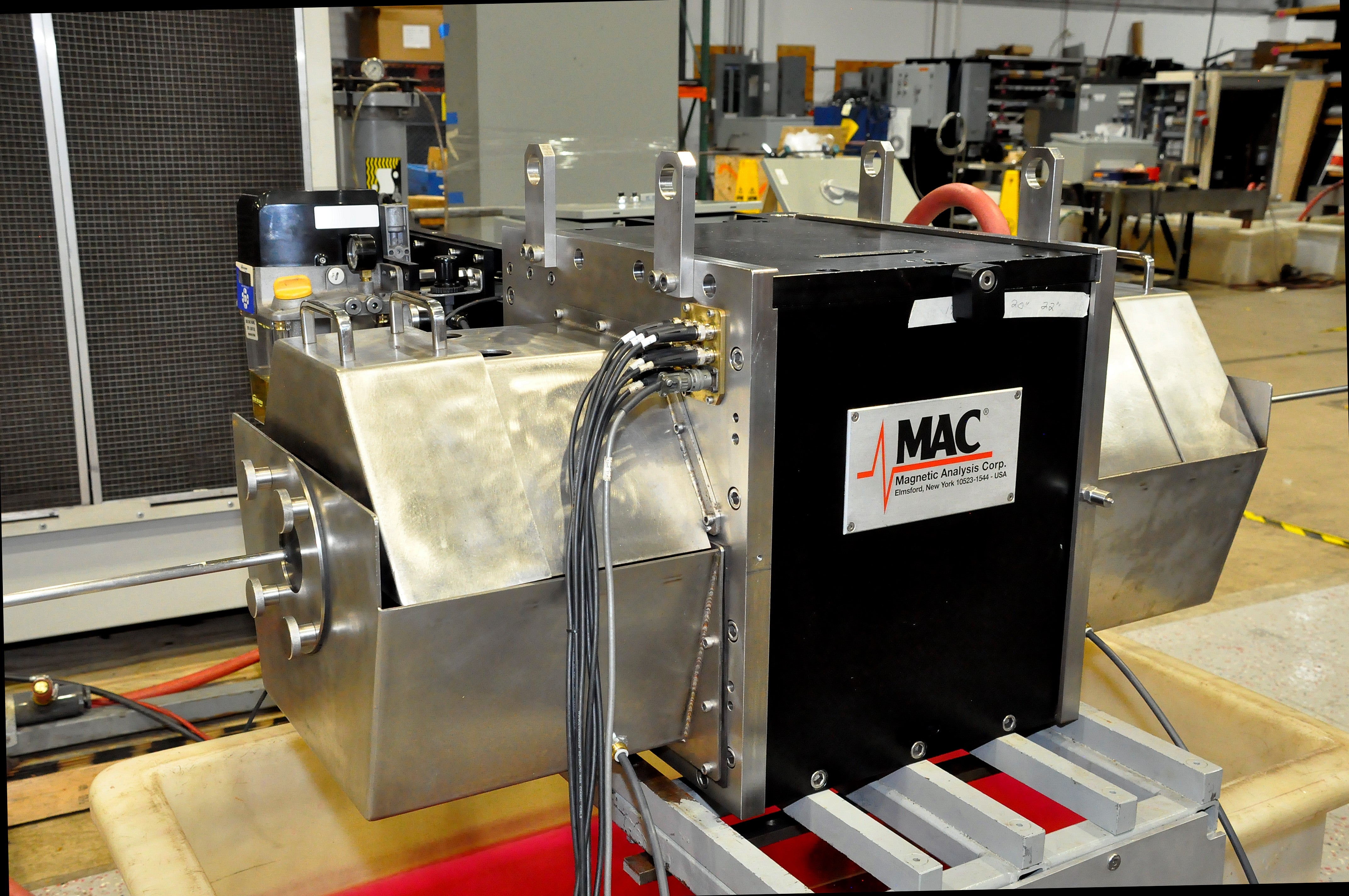
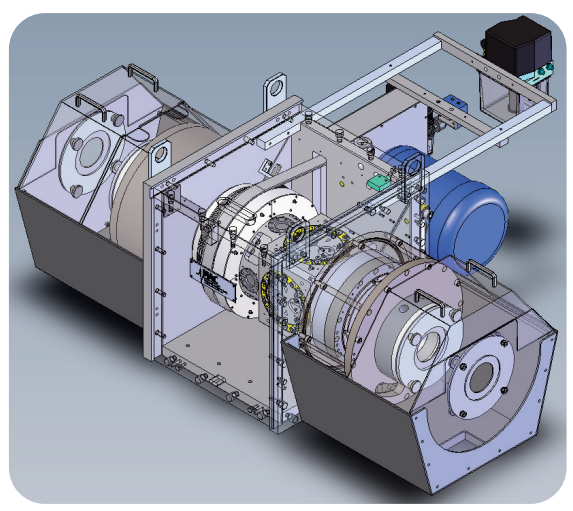
Ultrasonic Rotary Mechanism for High Speed Testing of Round Bar and Tubular Products
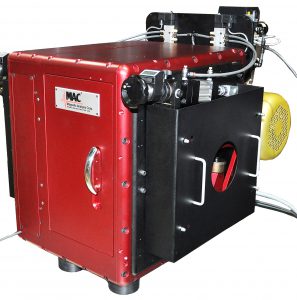
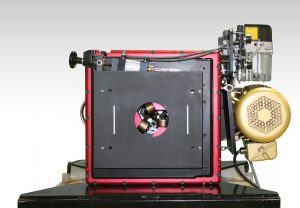
Flux Leakage Tester for Detecting Surface Defects in Hot Rolled Black Steel Bar
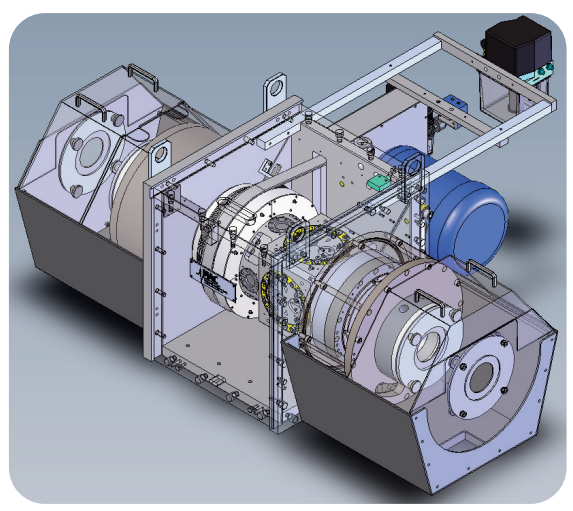
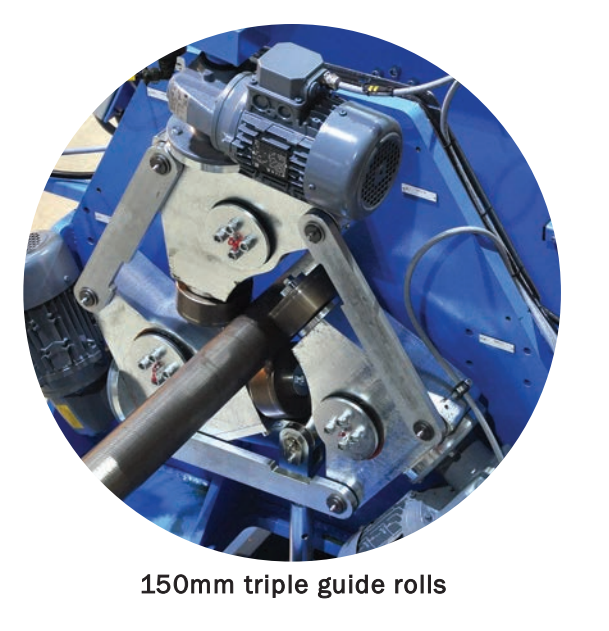
Ultrasonic Rotary Mechanism for High Speed Testing of Round Bar and Tubular Products
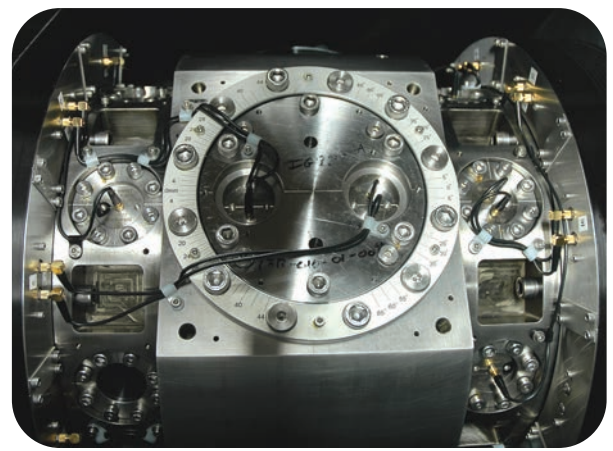
Ultrasonic Rotary Mechanism for High Speed Testing of Round Bar and Tubular Products
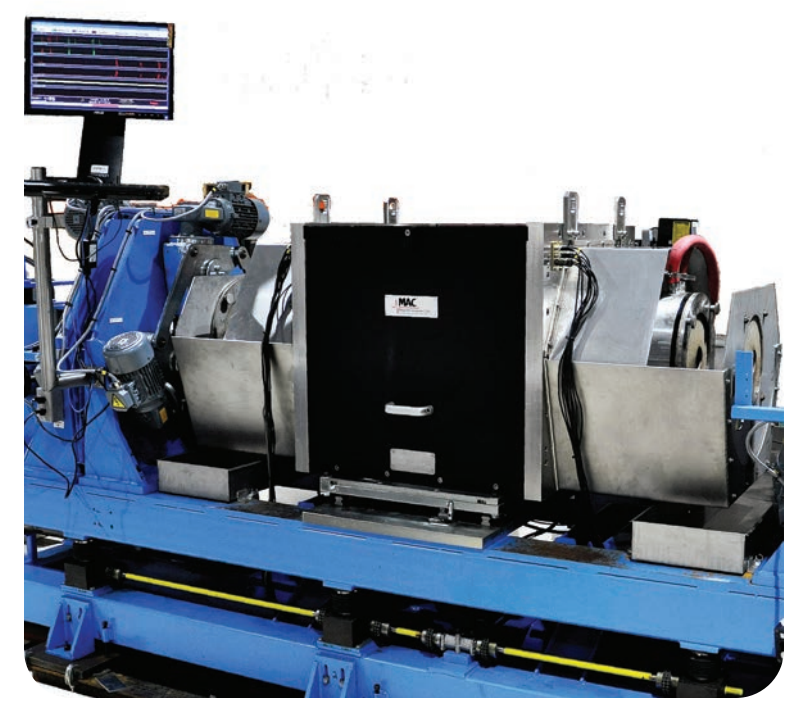
Ultrasonic Rotary Mechanism for High Speed Testing of Round Bar and Tubular Products
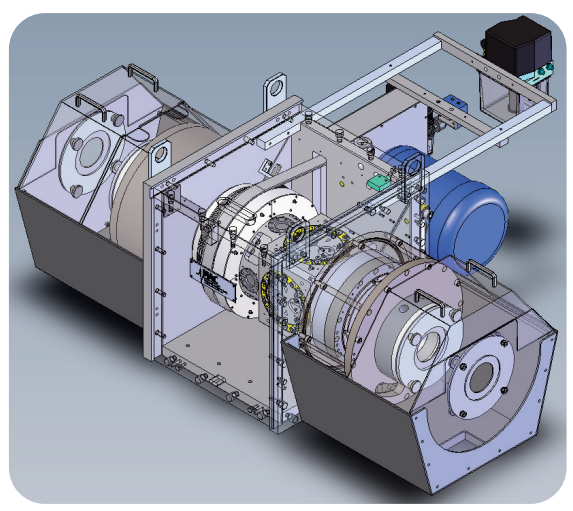
Ultrasonic Rotary Mechanism for High Speed Testing of Round Bar and Tubular Products
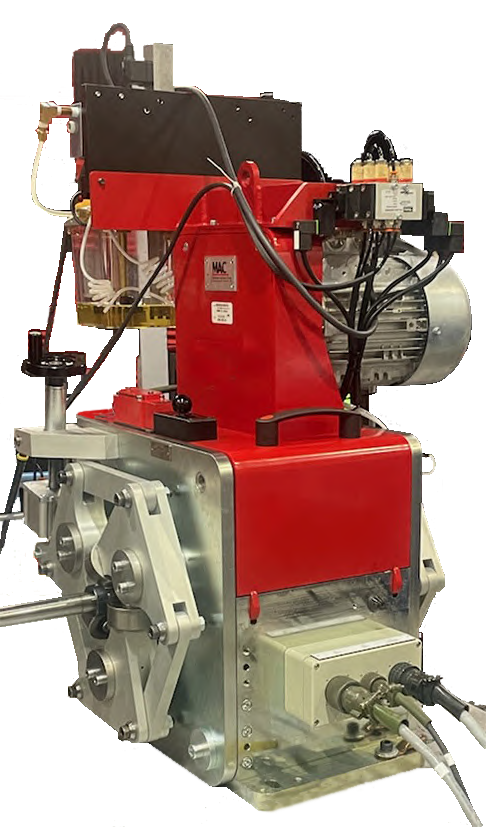
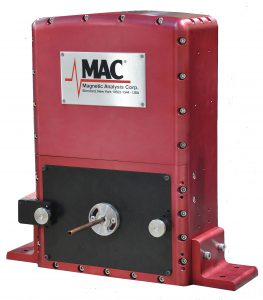
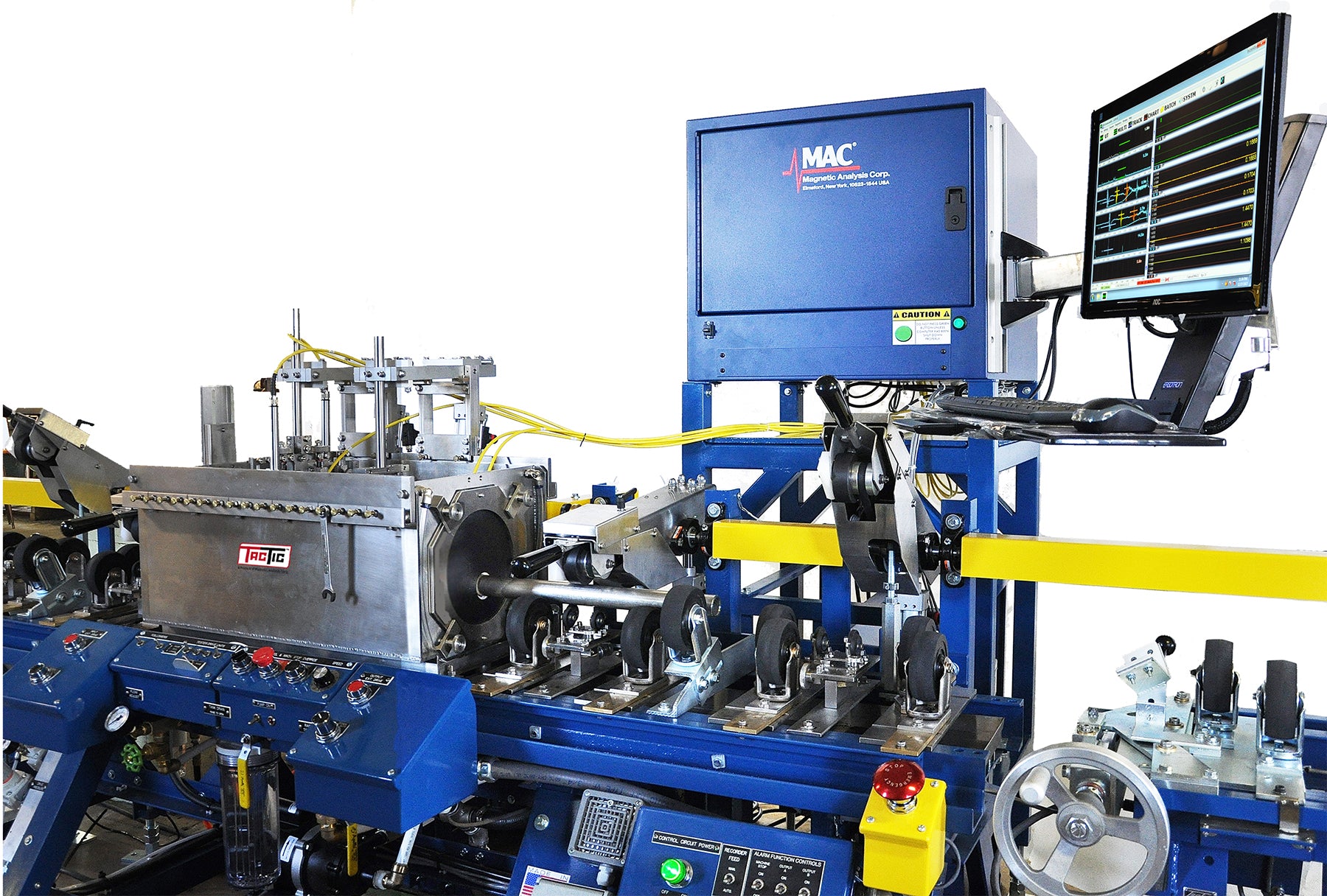
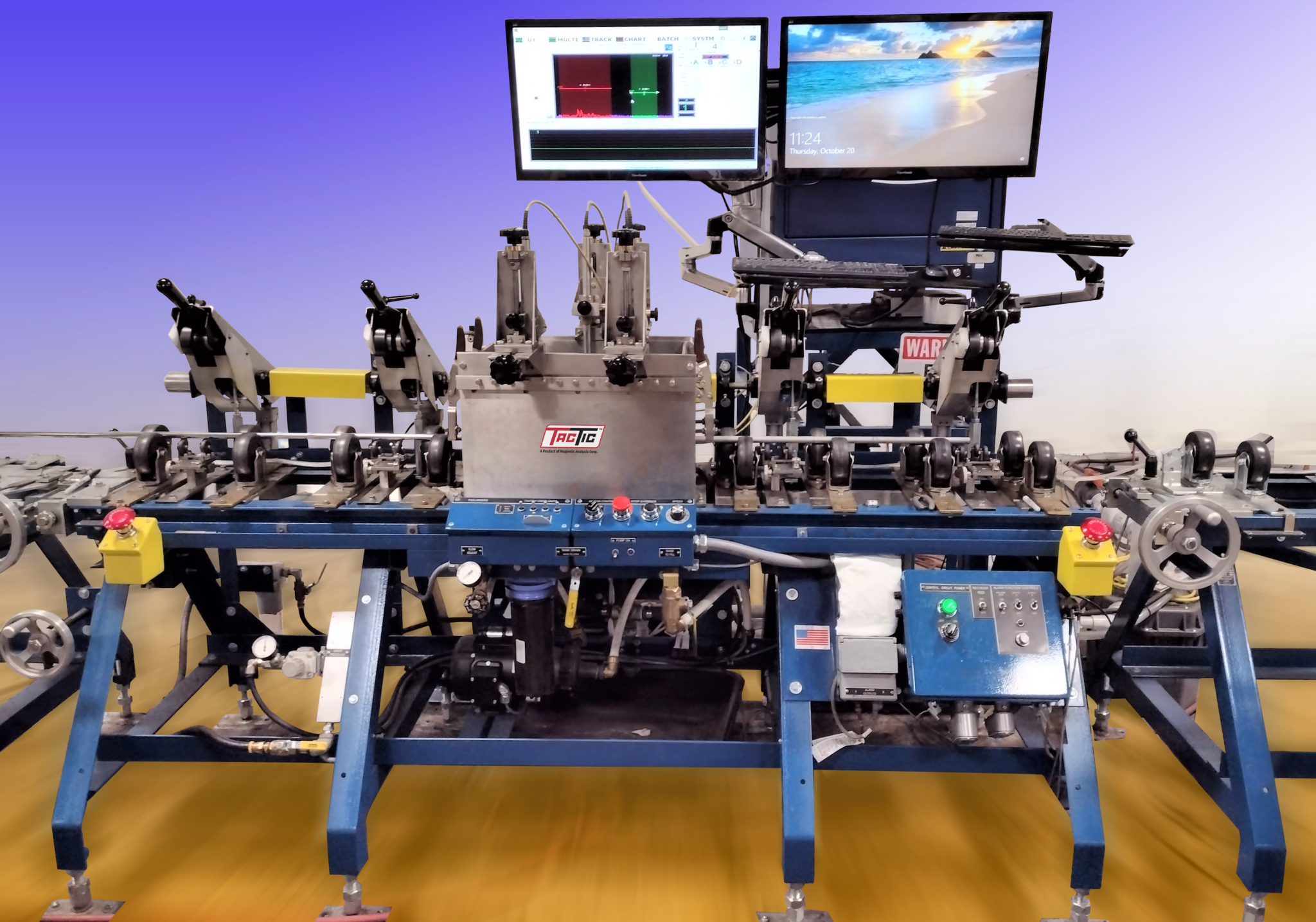
These rugged conveyor sections are placed at each end of a tester to provide good support for incoming and outgoing pieces.
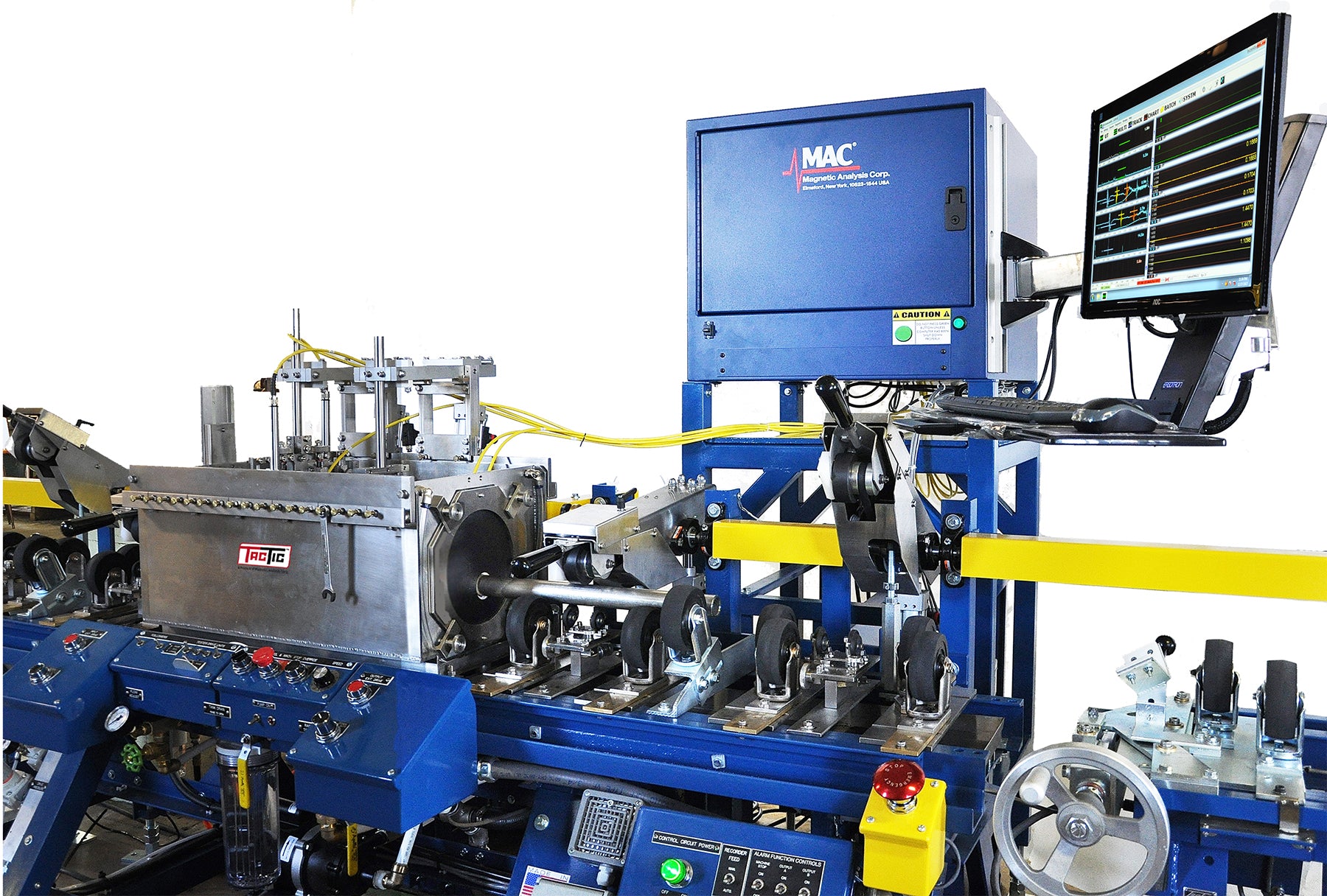
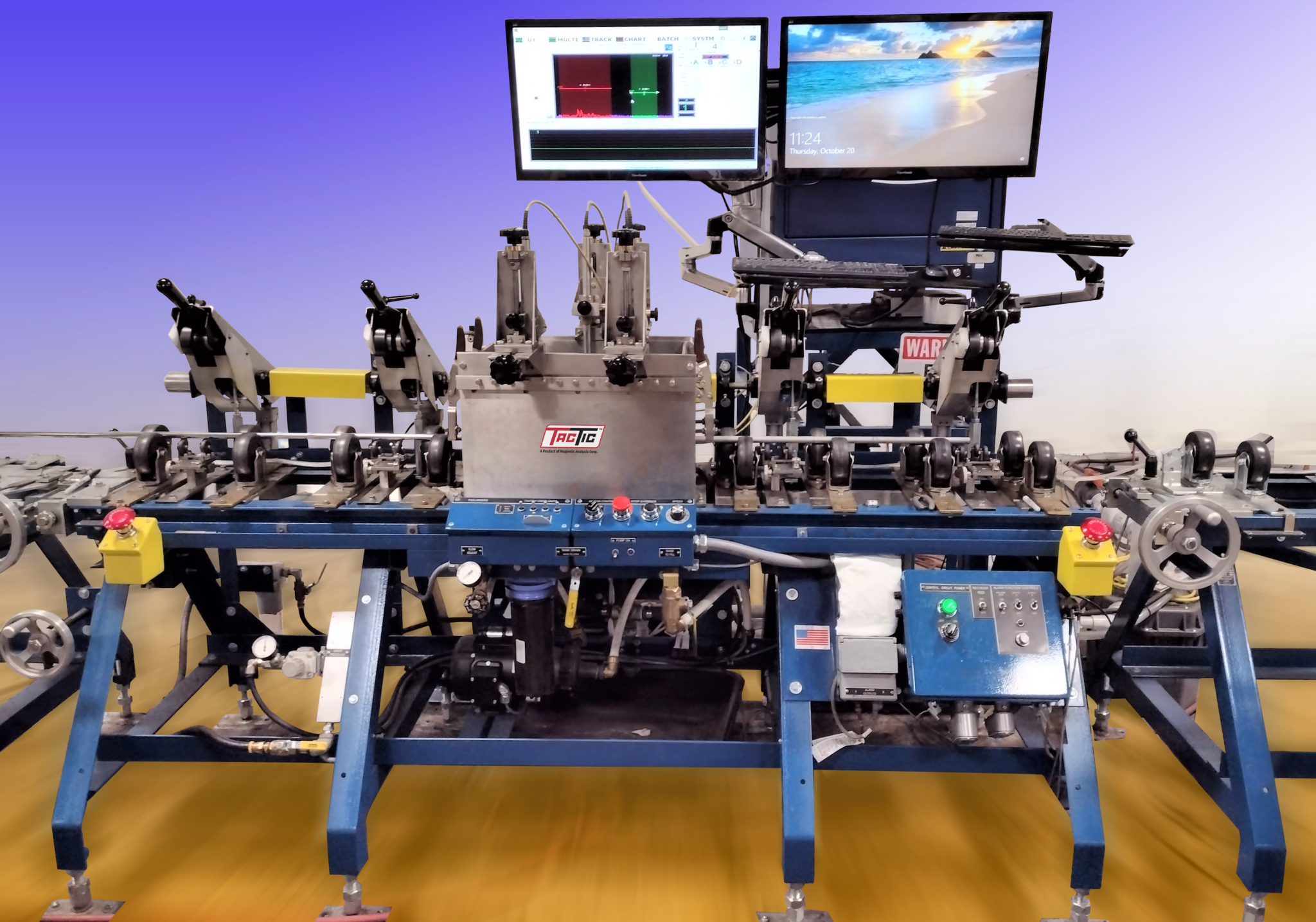
Model 76E “Standard Duty” Testers feature tanks with an inside length from 6″ to 30″ (150-760 mm).
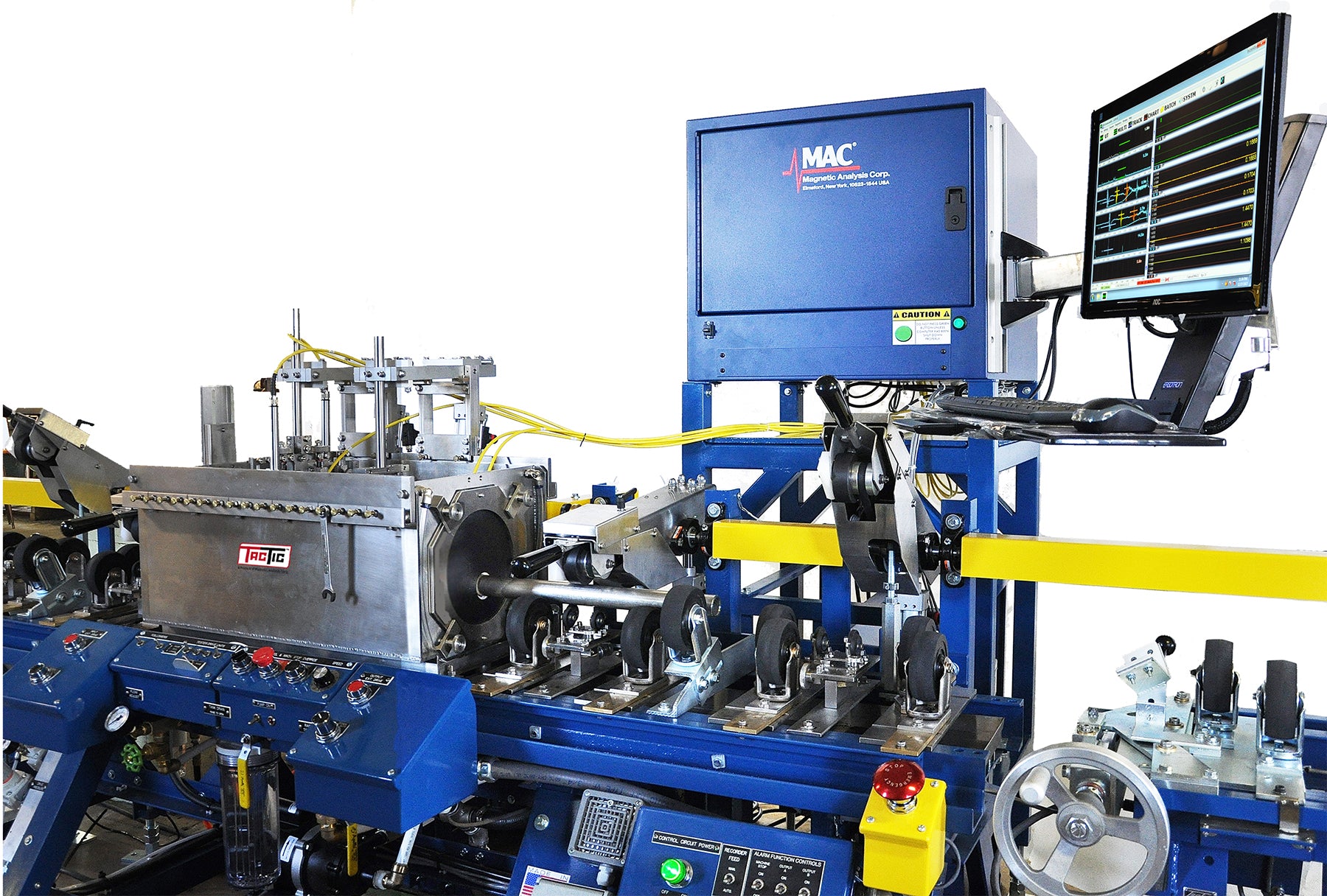
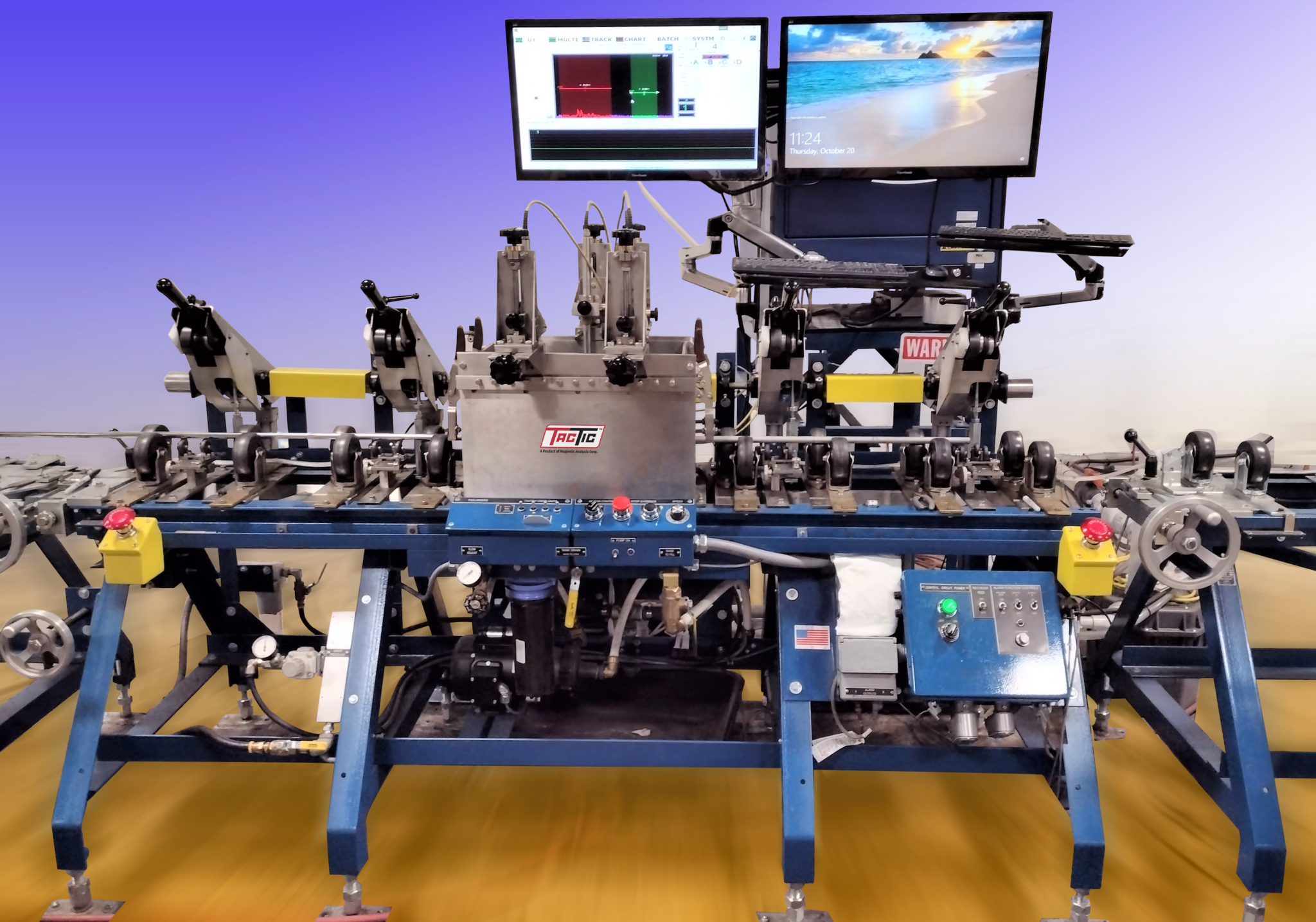
“Heavy Duty” Testers are powered either by a 7.5 HP motor (76F) or by a 10 HP motor (76G).
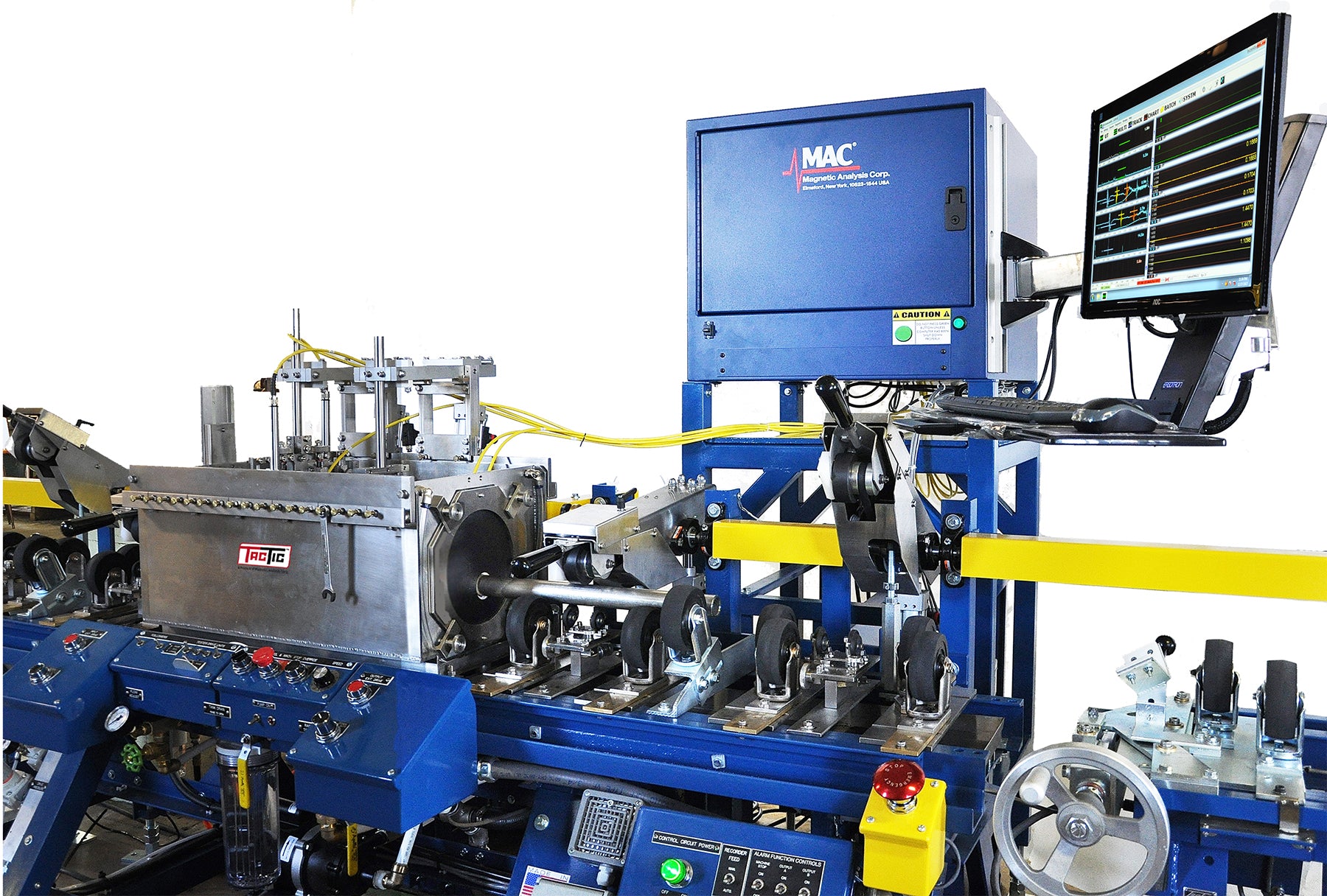
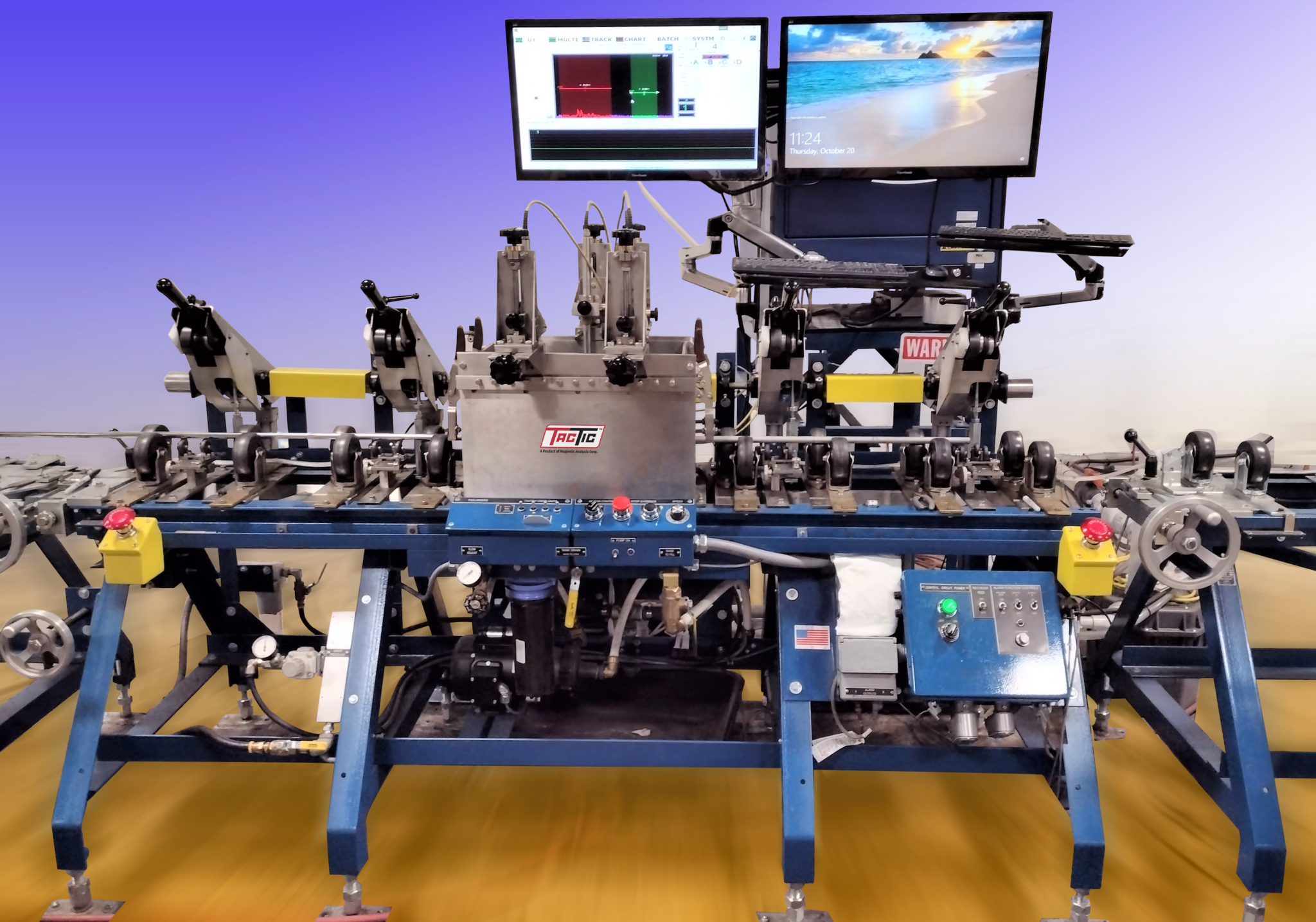
Ultrasonic Inspection Systems for Flat-Sided Material Squares, Rectangles, Hexagonals, Strip